The cotton harvest is in full swing. The one time of the year cotton farmers do not want rain is during harvest, and the ongoing drought has been very accommodating.
Harvesting and gin processing machines depend on the fluff and light weight of the lint to separate it from the leaves and other debris.
This year was a good time to see all three of the major techniques for accumulating cotton in the field. The standard method involves the combine, boll buggies and module maker.
The combine collects the lint from the cotton plants and accumulates it in its hopper. The combine then off-loads the lint into a boll buggie, which is a tall cart pulled by a tractor.
The boll buggie takes the lint to a module maker, which is a large box with no top or bottom into which the lint is dumped from the boll buggie and packed from the top by a large tamp.
Once the module is full and tightly packed, the sides swing away and the module maker is pulled off, leaving a module of cotton that looks like a large loaf of bread. A large tarp is wrapped over the top of the module to keep it dry until it is picked up by a truck and taken to the gin for processing.
This standard process takes a lot of labor. The combine operator, boll buggie tractor drivers, module maker operator and truck driver all are needed to get the cotton from the field to the gin.
The next evolution involves a combine that not only accumulates the cotton, but also tamps it into a module about one-third the size of a standard module. The combine operator can off-load the module in the field himself. The labor then has been cut down to only three workers: the combine operator, a worker to cover the module and the truck driver.
The third and newest method is being produced by John Deere. The combine not only packs the cotton, but it also rolls it into a round bale and wraps it before rolling it off into the field. So now the labor has been reduced to just two: the combine operator and the truck driver.
These improvements have cut the number of workers needed to harvest and deliver cotton to the gin by half or better. But the equipment to get those savings is more expensive. With cotton combine prices starting at a half million dollars, not just anybody is trusted to operate one.
The next stop for the cotton is the gin. Around here, our cotton goes to the gin in Brooklet. The first thing you will notice about the gin is it is loud. At the gin, the module is pulled apart into tiny bits, and the leaves and other heavy debris is separated from the lint. Then another machine pulls the seed from the lint.
Neither of these processes is perfect. Some leaf matter is still present. Some dust and dirt gets by.
There are two grades of cotton produced. The highest grade is the clean, white cotton we are used to seeing, but packed into 500-pound bales and stored in a warehouse that looks like the one at the end of Indiana Jones and the Lost Ark. The second grade of cotton is gray from the dirt and has pieces of leaf and stem that did not separate. This grade of cotton gets used in mattresses and other bulk cotton products.
The cotton seed is stored in a huge pile in a separate building and is loaded raw into tractor trailers to be hauled for milling into cotton seed meal, sold whole or pressed into oil. Most of it finds its way back into cattle feed.
But the most surprising product to an Ohio boy like me was the gin trash. Gin trash is just what it is. No euphemisms here. Just like the lint lining the roadsides during harvest, there is a dusting of lint inside the processing barns. The lint has to be swept up. The lint and all the leaves, twigs and dirt separated from the cotton during processing are loaded into long field wagons supplied by cattlemen.
Once they are full, the farmers pull the trailers back to their cattle. Cars following the trailers as they rumble down the road might start out tailgating but soon back off a quarter mile to avoid the dust coming off the trailers.
As Bob Floyd explained all this to me, I had to ask if his cows actually ate this stuff.
“Yeah, at first they turned their noses up at it, but after they got a taste, it was hard to keep them out of it,” he said. “Once they eat all they can reach, we have to get in there and push the middle to the edge. It’s the dirtiest job on the farm. It is the last thing we do in the work day because you really need a shower once you’re done.”
Incredible! Absolutely nothing is wasted — not even the dirt and trash.
It is an interesting and intricate web of products that affect several different types of agribusiness. It’s not the simple family farm of Green Acres propaganda. The engineers, economists, agronomists, geneticists, epidemiologists, mathematicians, marketing professionals, meteorologists, hydrologists, bankers and insurance professionals — and a couple dozen other professions I have not mentioned — all work together to bring us the highest standard of living on the planet.
Cotton is but one example. Americans spend one-fourth of their income on three meals a day. The rest of the world spends half their income on two meals a day.
It is the low cost of food that has allowed us to have the disposable income to buy things like iPods, computers, cars, nice homes, vacations, boats and other toys.
On the national level, it makes our clean environment possible. Without the available disposable income, we as a nation could not afford the environmental programs and regulations we have today.
Poor countries suffer from polluted environments because they literally do not have the money to afford a clean environment.
We have had it so good for so long that some among us seem to have forgotten who makes all this affluence possible. Not to worry. I am glad to remind you.
Gardner lives in Keller. He is the UGA extension agent for Glynn County and also serves South Bryan. He can be reached at dgardner@uga.edu.
Cotton takes long journey from field to gin
Where the grass is greener
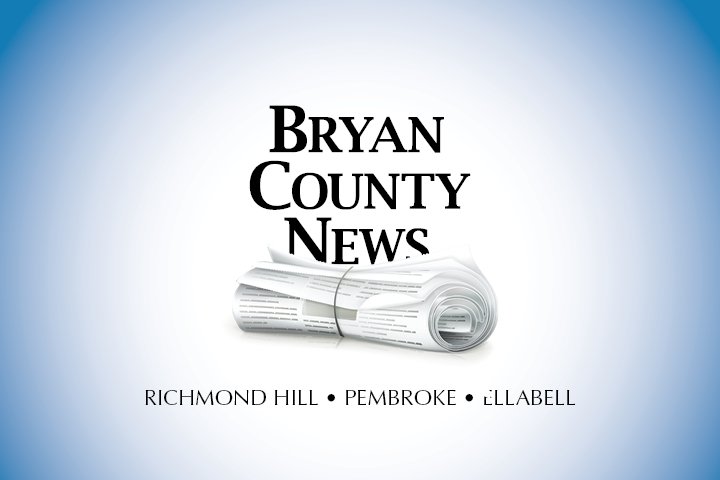
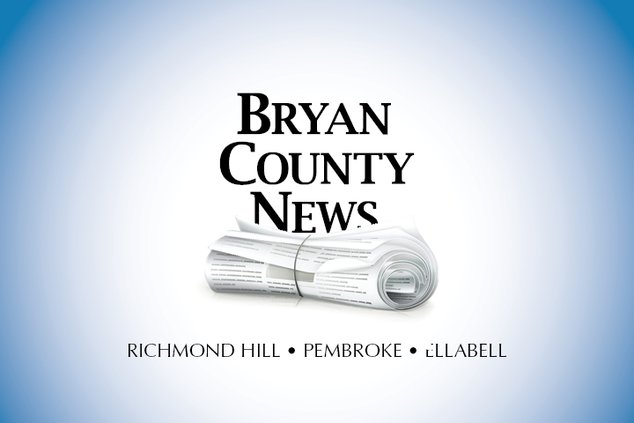
Sign up for our E-Newsletters